LCM·셀 생산기법 등 끊임없는 생산혁신으로 생산성 배가
[티후아나(멕시코)=뉴스핌 유효정기자] 미국 샌디에고에서 버스를 타고 30분 가량 달리니 도시의 풍광이 사라 진다. 미국과 멕시코 국경을 넘어선 것이다. 차창 밖으로는 나즈막한 산 중턱에 촘촘이 지어진 ‘지붕없는’ 집들이 즐비해 있다.
“지붕까지 지으면 세금을 내야 하기 때문에 지붕은 짓지 않고 그냥 살아요, 비도 거의 안오니까”
‘국경’을 사이에 두고 극심한 빈부의 격차를 눈으로 확인할 수 있다고 말한 이 가이드에 따르면, 멕시코 국경 지역은 몇 사람 죽어도 큰 일이 아닐 만큼 치안이 불안정하다.
위험한 이곳 멕시코에서도 ‘삼성’의 입지만큼은 특별하다.
경찰이 차량에 올라타 여권을 일일이 검사한 후 통과해야 한다는 멕시코 입국 관리소도 ‘삼성’에서 온 사람들이라는 이유로 검사 없이 일단 통과.
버스를 탄 채 15분 가량 더 달리니 국경에서 20km 떨어진 멕시코 최북단 티후아나 시 소재 '엘 플로리도 (El Florido)' 공단에 진입했다.
가장 먼저 눈에 띈 것은 익숙한 푸른색의 삼성 로고.
이곳에 위치한 삼성전자 멕시코 생산법인(SAMEX)은 8만4000 평에 3100명의 임직원이 근무하는 엘 플로리도 공단 내 최대 규모 생산기지다. 5년 연속 삼성전자의 미주 TV시장 1위를 가능하게 한 전초 기지 역할을 한 곳이다. 함께 입주해 있는 삼성SDI의 66000여평 규모를 더하면 전체 삼성이 차지하고 있는 면적은 15만평에 달한다.
삼성전자의 TV 전체 물량 가운데 20% 이상이 이 곳에서 탄생한다. 지난해 성수기에는 하루 평균 7만대, 비수기에 4만 5천대 가량 생산한다. 46인치를 주력으로 65인치도 소량 생산하며 올해 32인치 이상 전제품을 생산할 계획이다.
3D·LED·LCD·PDP TV, 그리고 블루레이 플레이어와 홈 시어터 등 AV 제품과 모니터도 생산해 미국뿐 아니라 캐나다, 멕시코, 브라질, 아르헨티나 등에 광범위하게 공급하는 현재 TV 해외법인 가운데 최대 규모다.
SAMEX의 총 3100명의 임직원 가운데 한국인 주재원은 고작 14명에 불과하다. 철저한 현지화를 이룬 이 곳의 ‘삼성’ 고용창출 효과는 약 9596명(SAMEX 3199명, 삼성SDI 869명, 협력사 5528명)에 달한다.
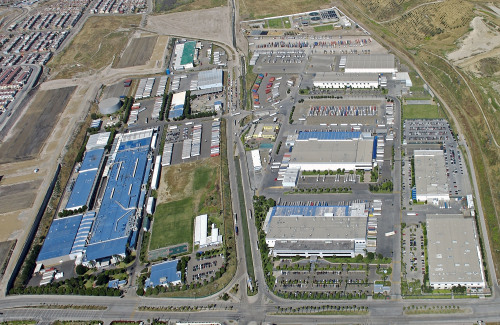
◇ 美 시장 1등 이끈 ‘생산 혁신’ - 리퀴드크리스탈모듈(LCM) 생산 도입
이곳의 끊임없는 ‘생산 혁신’은 더 가격 경쟁력 있는 제품을 베스트바이 등 미국 유통점에 단납기로 적기에 공급해 시장 점유율을 늘리는데 기여한 일등 공신이다.
대표 적인 것이 셀(CELL) 생산과 LCM(Lipuid Crystal Module) 생산 방식의 도입이다.
작년 8월, 이곳 SAMEX는 LCD 모듈을 직접 생산하는 LCM 생산 방식을 도입했다. 기존처럼 ‘제작된’ LCD 패널을 받아 조립해 TV로 생산하는 방식이 아니라 현지 부품업체들에서 조달받은 부품을 투입해 LCD 셀과 백라이트(후면 광원)을 직접 만들고 최종 TV 조립까지 ‘한번에, 한자리에서’ 만들어내는 일괄 생산 방식이다.
이 생산방식을 도입하기 위해 백라이트 생산 인원 등을 포함해 345명이나 더 뽑았을 정도로 대대적인 변화가 일어났다.
이 곳에서 생산되는 PDP TV 생산라인도 부품 상태에서 셀-모듈-TV로 이어진 ‘일괄생산’ 방식을 갖췄다.
이처럼 한 자리에서 모두 만들어지는 TV 생산방식을 도입한 이유는 적기 납품력과 원가 경쟁력을 동시에 갖추는 비결이다.
김석기 SAMEX 법인장(상무)은 “북미 시장 점유율을 늘리는데 ‘단납기’ 경쟁력이 크게 일조를 했다”며 “베스트바이에서 일주일 전에 주문을 줘도 ‘무조건’ 맞출 수 있다”고 설명했다.
‘한 자리’에서 만드니 따로 부품을 공수하는 과정에서의 지연, 또 패널과 셀의 이송과정의 물류 등이 발생하지 않기 때문이다. 김 법인장에 따르면 ‘셀(패널의 반제품)’ 상태에서 바로 공수해 오면 패널이 오는 비용의 1/5 가격에 불과하다.
김 법인장은 “심지어 한국에서 제품이 배를 타면 이 정보가 실시간으로 공유돼 우리가 베스트바이에 언제 납품할 수 있는지도 보여줄 수 있다”며 철저한 공급망관리(SCM) 경쟁력을 갖췄다는 것을 강조했다.
최근 LCM 라인 정밀화에 대한 설비 투자를 했으며 올해 상반기되면 대형 협력업체 2개를 포함한 부품 인프라까지 갖추고 하반기 이후 LCM 라인을 풀가동할 계획이다.
◇ 사라진 컨베이어…‘조를 이룬 몇 사람이 한 자리에서 완결하는 ‘셀(CELL)’ 생산’
사실 이 곳의 SCM 혁신은 2007년 ‘셀(CELL)’ 방식 생산 도입을 통해 큰 변화를 맞았다.
셀 방식이란, 패널·PCB 등 주요 부품들이 모듈 형태로 제조라인에 입고되면, 숙련된 작업자들이 2~3명씩 조를 이뤄 각자의 셀(일종의 공간)에서 조립부터 포장, 검사 작업까지 한꺼번에 수행하는 방식이다.
이 방식을 처음 도입한 3년 전과 비교해 생산량은 30% 늘어났고 인력은 크게 줄었다. 적기 공급 능력도 한층 높아졌다.
바삐 돌아가는 셀 라인의 조립자들을 바라보던 김 법인장은 “120m 길이의 4개 컨베이어 벨트가 들어서 있던 자리에 컨베 단지 10개의 ‘셀 생산 라인’만으로도 기존 생산성이 4~5배로 증대됐다”고 뿌듯해 했다.
또 이 셀 방식은 각 공장마다 대형 TV 및 중소형 TV 등 조립 특성에 맞게 다른 모습으로 구성돼있다.
김 법인장은 “생산성 뿐만 아니라 셀 방식 도입은 작업자들의 전문성과 책임의식을 강하게 해, 품질도 눈에 띄게 좋아 졌다”며, “또한 최근에는 함께 진출해 있는 협력업체들의 경쟁력 강화 측면에서 적극적인 도움을 주면서, 제품력이 전반적으로 크게 향상되는 좋은 결과를 얻었다”라고 강조했다.
김 법인장은 “언제, 누가 조립했는지 다 나오는 ‘셋트 실명제’도 실시해 불량률을 낮췄다”고 소개했다.
▶ 글로벌 투자시대의 프리미엄 마켓정보 “뉴스핌 골드 클럽”
▶ 뉴스핌 Zero쿠폰 탄생! 명품증권방송 최저가 + 주식매매수수료 무료”
[뉴스핌 Newspim]유효정 기자 (hjyoo@newspim.com )